On the concrete surfaces suitable for making the industrial floor coating; the surface preparation is made in order to remove the low resistance grout layer of the loose particles and roughen the surface. The surface preparation should be made by shot blasting machine (Blastrac).
Usually, marble slimming machines and diamond tipped hand machines and rotatiger are used in the market. Marble slimming machine and diamond tipped hand machines do “slimming” in the micron range. Roughening is out of the question. The rotatiger is used to do roughening, but can not do the real roughening, only leaves the tatches on the floor in patches. Unfortunately, a surface preparation can not be performed as required via the usual methods. The surface preparation is the half of industrial floor coating work. Making an incorrectly surface prepared application similar to a construction with a non solid foundation is not wrong at all.
One of the most important advantages of the shot blast machine; is both to remove the grout layer by roughening and to make the surface oil and dirt free and ready for the liner process.
A photograph showing where the machine passes and does not pass.

A typical photograph showing pre and post-surface preparation

Every kind of dirt such as dust, paint, oil, grease, which will reduce or hinder
the adherence, should be cleaned off from the surface. If there are layers where the oil
has deepened through, these layers may need to be removed. The polyurea can not be applied to the oily surface. The surfaces are made robust, clean and rough.
An area, of which surface preparation is completed.
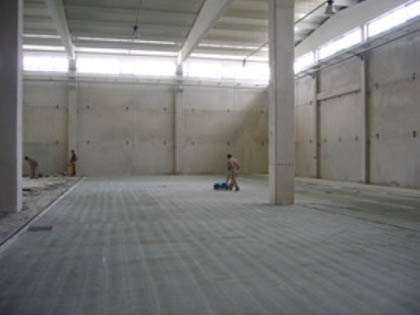
Another view
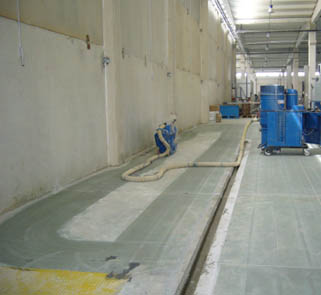
Mask51 application will be made to the prepared surfaces at the next stage. Mask51 is a bonding layer between polyurea and the surface on which the polyruea to be applied. In order for the liner to work properly, adhere to the concrete, it is crucial that the surface preparation should be made in accordance with its specification. Therefore, we say, “the surface preparation is the half of industrial coating work”.
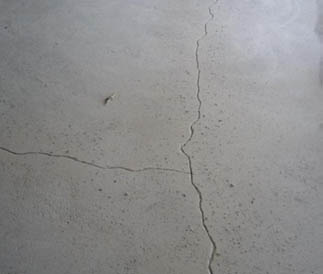
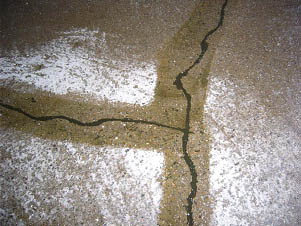
The surface crack repaired by Mask51.
Application Definition:
The cleaned, crack and the joint repaired concrete surface without any humidity and water concerns, is made suitable for coating Mask51. The Mask51 liner is applied to the surface. After the Mask51 is impregnated on the surface as a single layer by a roller, the silica and the quartz is spilled upon the Mask51 impregnated surface. Mask51; fills up the spaces, increases the impact and the chemical resistant of surface, at the same time makes the following layers adhere to the surface. After the surface and joint repair is completed, The Mask 51 liner application is made.
The area where Mask51 application is completed.
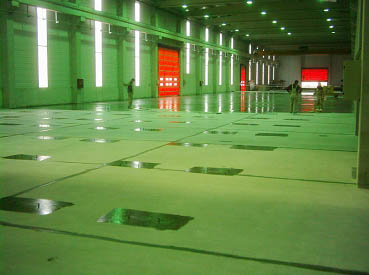
The area where Mask51 application is completed.
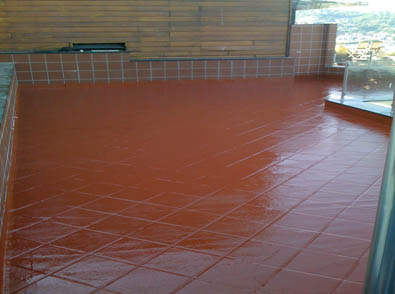
Terrace Polyurea Coating
